Since its foundation DK Coatings has been a combination of curiosity, ambition, inventiveness and strong adaptable teamwork. Together with our specialists and partners we have been developing coatings for the present and the future for more than 20 years from the idea to the suitable product solution.
With expertise and curiosity for new solutions
Development
PHILOSOPHY AND MOTIVATION
From the idea to the
product
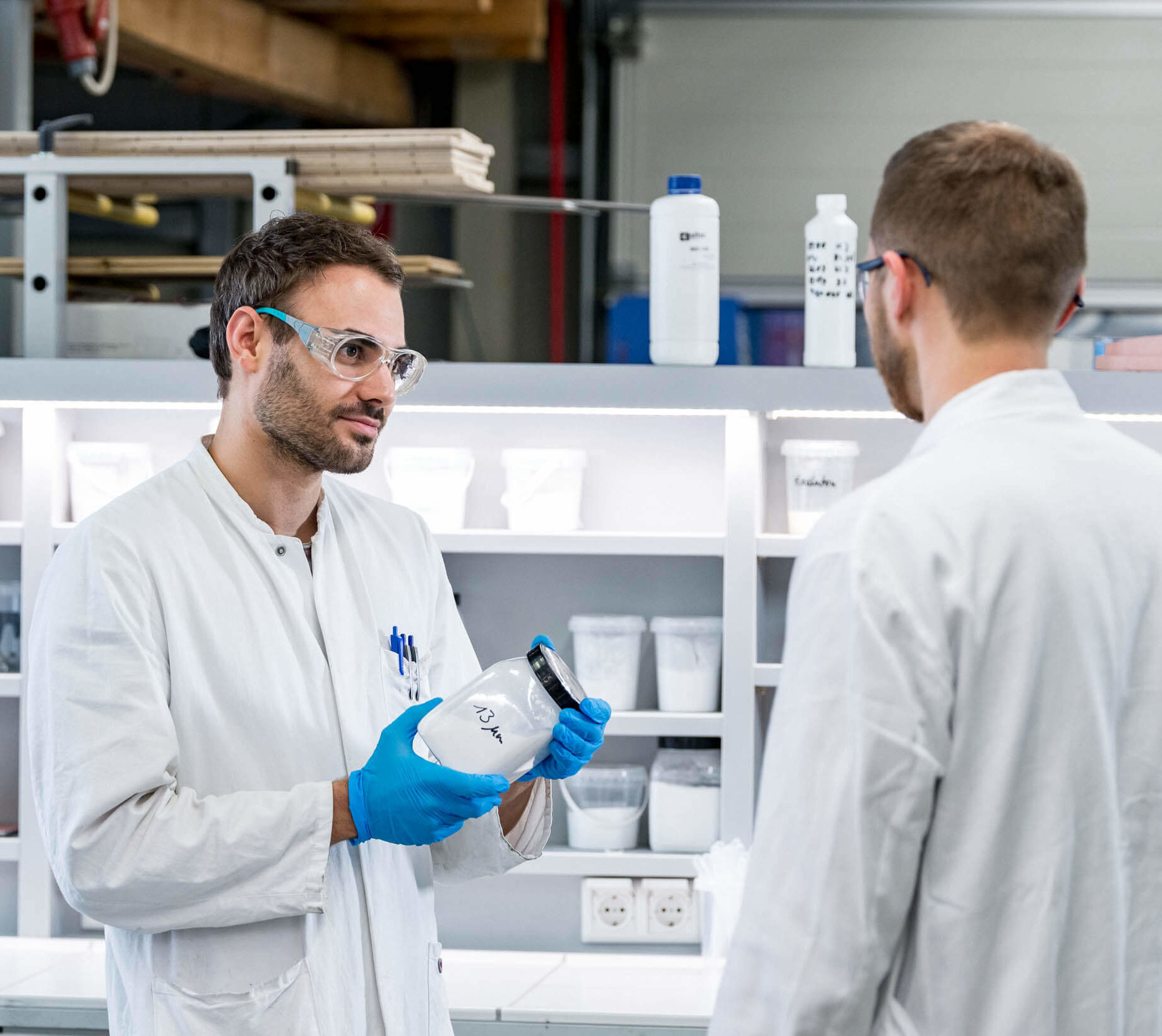
DEVELOPMENT PROCESS
Future-oriented and individual Product Development
Individual consultation and product development
QUALITY ASSURANCE
Quality analysis and testing methods of the DK Coatings Laboratory
PH level determination
Density measurement
Viscosity
determination
Surface Measurement
By measuring the surface tension, the quality of the adhesion can be determined in real time. The polarity of the product is also important for the quality.
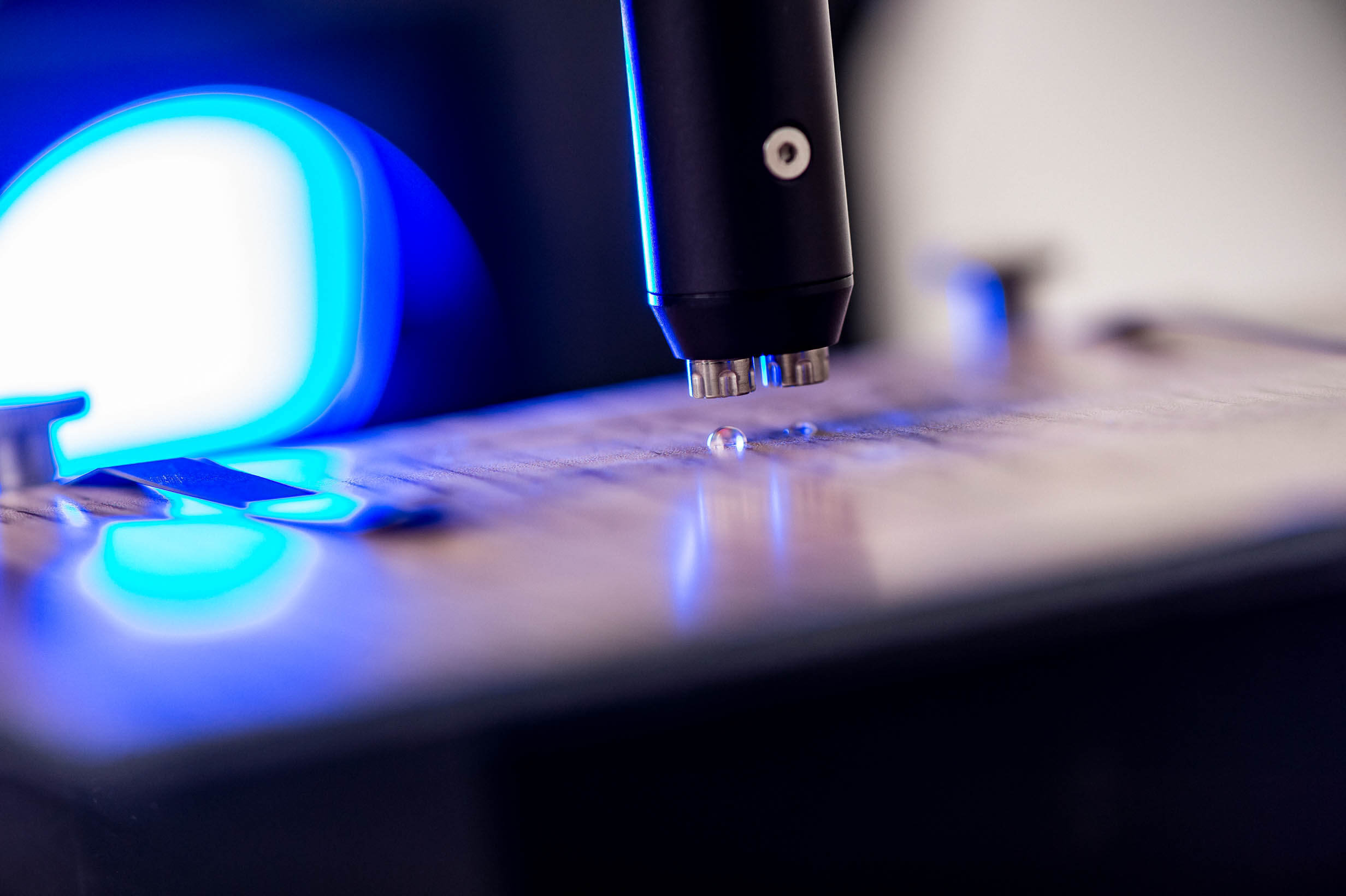
camera
dosing nozzle
product
QUALITY CONTROL
Quality controls and coating processes in the DK Coatings Technical Center
The DK Coatings Technikum is one of the central facilities for product development and serves above all for quality control. As part of our service we carry out different test methods according to standards or based on standards. Part of the Technikum is also the quality control on site. For testing our coating systems in the customer's factory, we use mobile application equipment or UV lamps. The on-site tests are also to be considered as initial tests for internal purposes and do not exclude independent tests.
Weathering Tests
Weathering tests serve as a tool for improving product quality. Outdoor weathering is used to determine the resistance of coatings to external environmental influences.
Artificial weathering
according to DIN EN ISO 16474-1 / 3
This test method is used to examine the weather resistance of surfaces. In a special weathering chamber, samples are exposed to UV light, humidity and temperature and the changes in the surface are examined at regular intervals.
Cross Cut Test
In the cross cut test, two multiple cuts are made at a 90° angle to each other on a coating using a cross cutting device. This targeted damage to the surface allows conclusions to be drawn about the adhesion to the substrate.
Abrasion Resistance
The abrasion resistance of a coating is investigated with the help of rotating rubber rollers. This standardized method makes it possible to compare the abrasion resistance of different coatings with each other or with each other.
Double Rub Test
The “double rub test” is used to examine paint surfaces for solvent resistance. It is also used to test the cross-linking of UV coatings. In this test, a special felt is impregnated with e.g. methyl ethyl ketone (MEK) and rubbed in double strokes over the sample to be tested at a defined test force. The test duration depends on the occurrence of a visible change in the coating surface or the agreed number of double strokes.